La baisse régulière des consommations d’énergie de l’industrie française depuis une quinzaine d’années s’explique principalement par la crise économique, la délocalisation des secteurs gourmands en énergie, et la réorientation vers des activités d’assemblage (et non plus de production) de biens d’équipement ou même des activités tertiaires. Mais cette baisse reflète également la poursuite des progrès d’efficacité énergétique à l’œuvre depuis des décennies dans les processus de production.
Malgré ces efforts, le potentiel technique d’économies d’énergies dans l’industrie demeure encore important, à la fois grâce aux nouvelles performances des moteurs, de l’éclairage et des process spécifiques et par le développement du recyclage. Contrairement à l’idée selon laquelle toute nouvelle baisse de la consommation d’énergie de l’industrie ne signifierait qu’une perte d’activité, des gains de productivité importants sont accessibles grâce à de nouvelles actions de réduction de cette consommation, dont les temps de retour sur investissement sont souvent très faibles.
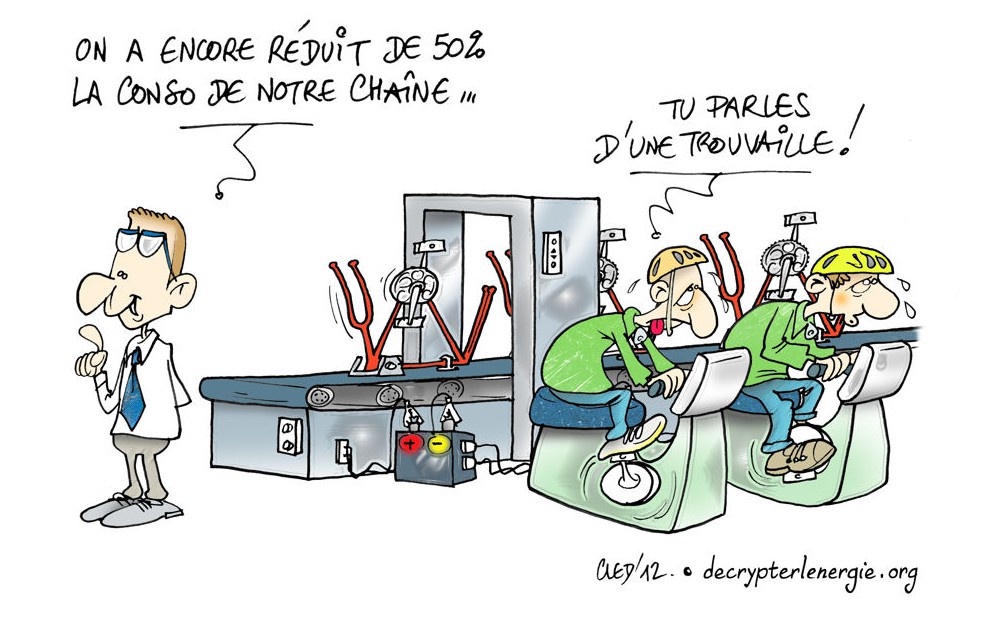
La consommation d’énergie du secteur industriel : de quoi parle-t-on ?
La consommation d’énergie que requiert la fabrication industrielle d’un bien de consommation ou d’un matériau est le produit de deux facteurs : la quantité à produire et l’énergie dépensée pour fabriquer une unité de ce bien ou de ce matériau.
Lorsqu’il s’agit de matériaux bruts, on rapporte directement la consommation d’énergie à la masse produite ; on parle alors de contenu énergétique. Par exemple, pour produire une tonne de ciment, il faut en France environ 1260 kilowattheures1 (kWh). Mais s’il s’agit d’un bien d’équipement (automobile, moteur, meuble, etc.), celui-ci met en jeu de nombreux matériaux, transportés, transformés, façonnés et assemblés, si bien qu’on ne se réfère plus directement à son contenu énergétique. On parle plutôt dans ce cas d’intensité énergétique, qui est rapportée à la valeur monétaire du bien. Par exemple, pour le montage d’une voiture, cette intensité énergétique est de 0,2 kWh/€2 en moyenne en France.
La baisse de la consommation d’énergie de l’industrie repose essentiellement sur trois causes , généralement combinées :
- une baisse, à modes de production constant, des quantités produites,
- un changement structurel privilégiant l’assemblage de produits à forte valeur ajoutée plutôt que la fabrication de matériaux bruts consommateurs d’énergie (transfert d’activité de l’industrie lourde vers l’industrie secondaire),
- une amélioration des procédés de production des matériaux bruts diminuant leur contenu énergétique, ou des procédés de production des produits intermédiaires ou finis.
Il est essentiel, lorsqu’on analyse l’évolution de la consommation d’énergie de l’industrie, de bien distinguer ces différents facteurs. Ainsi, une baisse de l’intensité énergétique peut aussi bien s’expliquer par un important effort d’efficacité énergétique dans les processus industriels que par la délocalisation à l’étranger des industries les plus gourmandes en énergie – avec évidemment des conséquences très différentes pour l’économie et la société.
Si le progrès technique s’accompagne partout d’une baisse tendancielle de l’intensité énergétique, l’évolution de la consommation d’énergie de l’industrie dépend, dans chaque pays, des choix de politique industrielle de celui-ci, tant au niveau de l’orientation de sa production que des efforts pour en accroître l’efficacité.
Un regard vers le passé
Dans le cas de la France, la consommation d’énergie du secteur industriel a connu une baisse de 40 % au cours des quarante dernières années. Celle-ci mesure-t-elle un déclin de l’activité de production ou bien une diminution effective de l’intensité énergétique ? Dans ce cas, s’agit-il d’une amélioration des procédés ou d’un changement structurel de l’industrie nationale ?
Depuis 1973, l’indice de production industrielle(IPI) français a doublé. L’intensité énergétique a, quant à elle, fortement diminué dans les années soixante-dix, puis n’a baissé que de 1,3 % / an, en moyenne, à partir de la fin des années quatre-vingt.
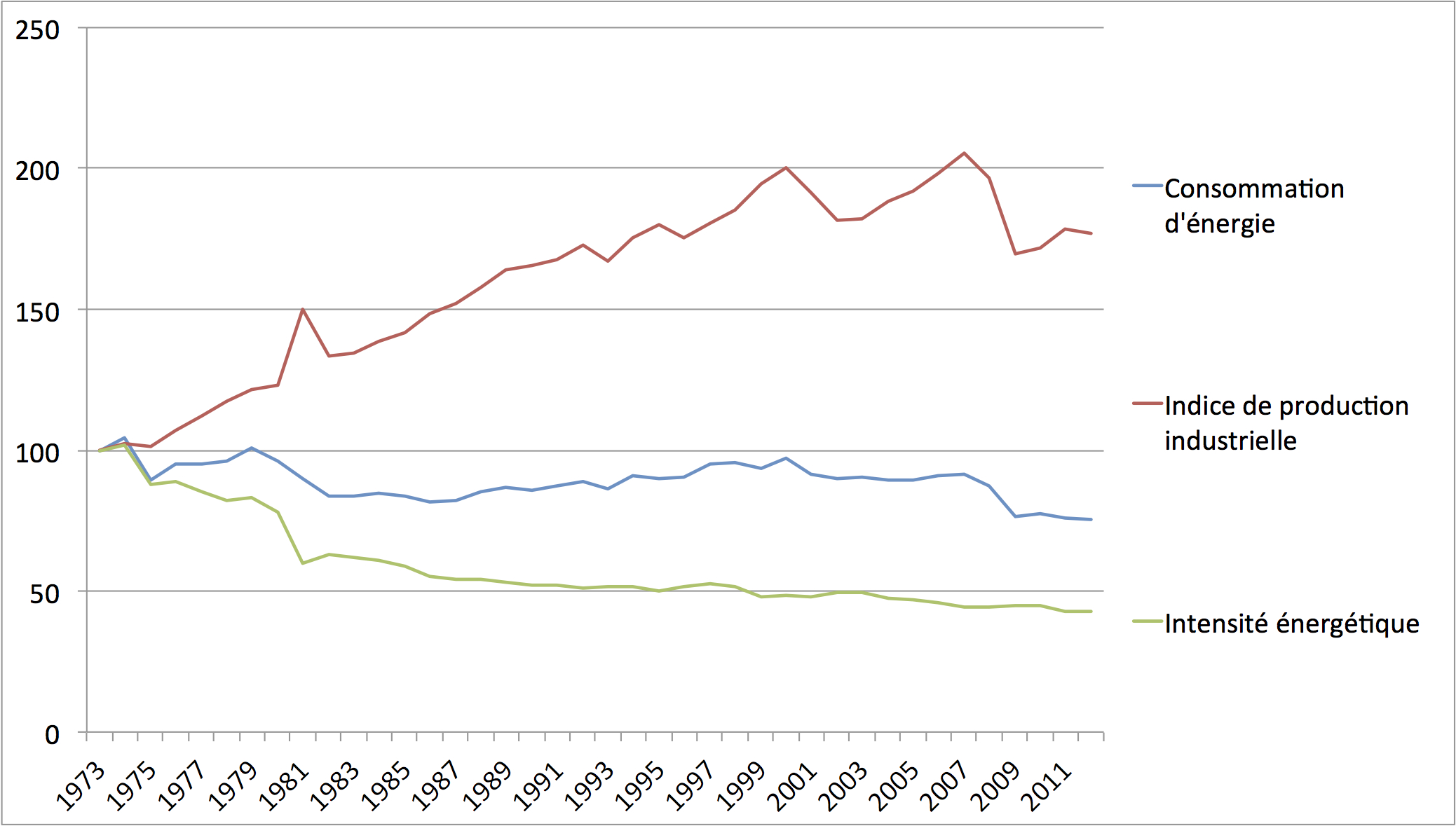
Figure 1 : Variation de l’Indice de production industrielle (IPI), de la consommation d’énergie finale et de l’intensité énergétique (base 100 en 1973) – Source : SOeS3, Insee4
Un regard plus attentif sur la période 1973-1986 montre que la sidérurgie est le premier secteur responsable de cette baisse de l’intensité énergétique (cf. figure 2).
En 1973, produire une tonne d’acier requérait 6500 kWh/t. Cette consommation a baissé fortement jusqu’au milieu des années 1980, avant de se stabiliser autour de 4500 kWh/t aujourd’hui. Outre l’amélioration des rendements des hauts fourneaux, l’introduction de l’acier secondaire (acier recyclé) issu des ferrailles explique cette diminution : l’acier recyclé ne nécessite que 1860 kWh/t soit 3,5 fois moins que l’acier brut. Malgré cela, il ne représente aujourd’hui que 50 % de l’acier utilisé en France.
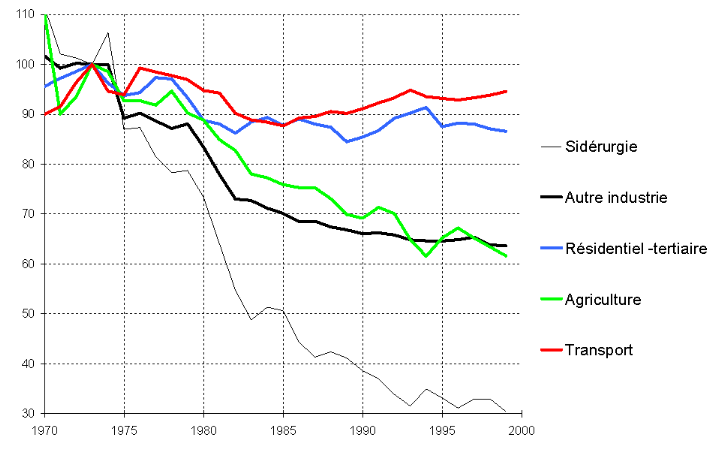
Figure 2 : Évolution comparative des consommations d’énergie en France dans différents secteurs industriels – Source : ministère de l’Économie, 20005
Pour l’ensemble des autres secteurs industriels, la baisse de l’intensité énergétique a deux causes : des gains de production grâce aux améliorations technologiques, mais également une réorientation structurelle vers des secteurs moins gourmands en énergie pour une même valeur ajoutée. Il est difficile de connaître précisément la part relative de ces deux causes et son évolution dans le temps. La figure 3 montre, sur la période 1986-2006, l’influence relative des différents secteurs sur l’effet de structure et l’effet technologique. On constate que la baisse d’intensité énergétique est autant due à une amélioration de l’efficacité des process qu’à une réorientation de la production plus favorable à des secteurs moins gourmands en énergie.
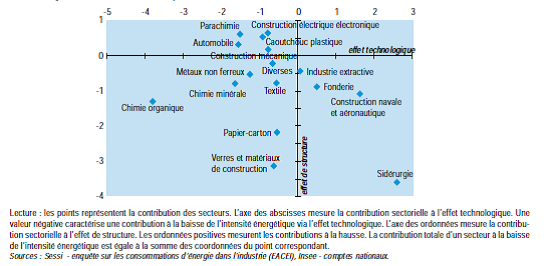
Figure 3 : Contribution de l’effet technologique et de l’effet de structure à la variation de l’intensité énergétique dans différents secteurs entre 1996 et 2006 – Source : Insee6
Un gisement important d’économies d’énergie
Si, dans le passé, la baisse de la production industrielle et les effets de structure ont contribué à réduire la consommation d’énergie de l’industrie française, les efforts d’efficacité énergétique ont également joué un rôle important. Toutefois, l’analyse de la situation actuelle montre qu’un potentiel élevé d’économies d’énergie supplémentaires existe encore. Celles-ci peuvent notamment venir d’une efficacité énergétique accrue des équipements utilisés dans les chaînes de fabrication ou en support des installations industrielles – on parle alors d’économies transverses, car elles sont communes aux différents secteurs industriels –, d’améliorations spécifiques des process de production les plus consommateurs d’énergie, et d’une réduction du contenu énergétique des matériaux par un renforcement du recyclage.
L’amélioration des moteurs, de l’éclairage et des chaufferies contribue dans tous les secteurs à un potentiel d’économies transverses conséquent. Une étude du Ceren7 montre qu’une grande partie de ce potentiel est mobilisable avec un temps de retour inférieur à trois ans. Le tableau ci-dessous montre que les moteurs électriques de toute nature ont requis 90 TWh en 2010 ; cette consommation pourrait être diminuée de 31 TWh, les deux tiers de cette économie étant mobilisable avec un temps de retour sur investissement inférieur à 3 ans.
Usage | Économie | Conso 2010 (TWh) |
Potentiel d’économie (TWh) |
Potentiel avec temps de retour < 3 ans (TWh) |
|
---|---|---|---|---|---|
Force motrice | Moteurs, ventilation | Transversal | 90 | 31 | 21 |
Thermique | Chauffage locaux | Transversal | 2 | 1 | 1 |
Thermique | Chaudières | Spécifique | 19 | ||
Elec. autre | Éclairage, froid, etc. | Transversal | 23 | 8 | 3 |
Elec. autre | Process | Spécifique | 7 | ||
Fabrication | Chaufferie et réseaux | Transversal | 18 | 13 | 10 |
Fabrication | Process | Spécifique | 194 | ||
Thermique | Chauffage locaux | Transversal | 23 | 12 | 11 |
Matières | Premières | Spécifique | 105 | ||
Prod.élec. | Cogénération | Transversal | 19 | Augmentation de la cogénération | |
TOTAL | 480 | 65 | 46 |
Il convient de compléter ces potentiels d’économies d’énergie par les économies spécifiques rendues possibles grâce à l’amélioration des process, secteur par secteur. Pour évaluer ces économies, on compare l’intensité énergétique moyenne d’une production donnée en France avec celle de l’usine la plus performante, ailleurs dans le monde. Par exemple :
Contenu énergétique (kWh/t) | Aujourd’hui en France | Meilleure pratique ailleurs |
Acier de haut fourneau | 6 300 | 4 900 |
Acier issu de ferrailles recyclées | 1 900 | 1 000 |
Aluminium primaire | 31 500 | 25 600 |
Aluminium recyclé | 1 500 | 950 |
Papier | 10 500 | 7 000 |
Papier recyclé | 3 300 | 1 630 |
Ciment | 1 300 | 700 |
Le tableau ci-dessus montre que non seulement il existe un gisement d’économie d’énergie pour chaque secteur (plus d’un tiers en moyenne) mais que la valorisation des déchets et leur recyclage augmente ce potentiel. En effet, d’une manière générale, le contenu énergétique des matériaux obtenus par recyclage est largement inférieur à celui de leur première production. Or ce gisement n’est actuellement exploité que partiellement (et parfois même très partiellement). Les taux de collecte des matériaux restent insuffisants, et les taux de recyclage estimés, même s’ils progressent, sont éloignés du potentiel de recyclage maximal estimé pour chacun des matériaux (qui dépend de différentes limites sur la qualité des matériaux, etc.). Une étude de l’Ademe9 fait l’état des lieux de cette situation, que nous résumons ainsi :
Taux de collecte 2010 | Taux de recyclage10 2010 | Potentiel de recyclage | |
---|---|---|---|
Acier | 74 % | 52 % | 90 % |
Aluminium | 44 % | 37 % | 86 % |
Verre | 35 % | 35 % | 90 % |
Plastiques | 15 % | 4,5 % | 30 % |
Papier carton | 70 % | 60 % | 80 % |
Différents facteurs expliquent ces faibles taux de recyclage, malgré l’intérêt évident, en particulier d’un point de vue énergétique, d’une réutilisation de ces matières premières. L’obstacle financier domine : il est souvent moins onéreux d’utiliser une matière première neuve que de mettre en place un système de collecte et d’investir dans de nouvelles unités de fabrication permettant le réemploi de matières à recycler.
D’autres freins, plus structurels, existent. Par exemple, dans la sidérurgie, l’emploi systématique d’acier recyclé nécessite de revoir en profondeur l’outil industriel. Les hauts-fourneaux ne permettent pas le réemploi de cette matière, seuls les fours à arc électrique le peuvent. Augmenter l’emploi d’acier recyclé, c’est donc diminuer le recours aux hauts-fourneaux français et supprimer de l’emploi dans ce secteur déjà fortement touché au cours des dernières décennies. Ce cas précis illustre la difficulté à allier deux volontés : maintenir l’emploi dans certains secteurs et diminuer la consommation d’énergie.
Encore plus d’économies d’énergie ?
Au-delà de l’important gisement d’économies d’énergie résidant dans une plus grande efficacité de la production industrielle, la consommation d’énergie de l’industrie peut aussi diminuer grâce à une baisse de la production dans certains secteurs, par la réduction des gaspillages. On peut en particulier penser aux suremballages très souvent employés dans l’industrie agro-alimentaire, sans justification de conservation des aliments.
Enfin, on constate depuis plusieurs années que la baisse des consommations d’énergie dans l’industrie est en partie due aux modifications structurelles, notamment à la délocalisation de certains pans de l’industrie. Cette évolution ne peut être assimilée à un effort positif d’économies d’énergie. On peut pourtant imaginer d’autres changements structurels dans la production industrielle française qui soient au contraire générateurs d’emplois pour le pays tout en s’inscrivant dans une logique globale de réduction de la consommation énergétique.
Conclusion |
Dans le secteur industriel, responsable de près de 20 % des émissions de CO2 françaises, de nombreux leviers restent à actionner pour réduire les consommations d’énergie. Les process et les équipements peuvent être rendus moins gourmands en énergie. Une utilisation accrue de matériaux recyclés permettrait, elle aussi, des gains substantiels. Ces réductions de consommations d’énergie rendraient l’industrie française plus compétitive, en diminuant – une fois les investissements dans l’efficacité énergétique rentabilisés – les coûts de production. Ce secteur serait également plus résilient, en étant moins impacté par les hausses du coût de l’énergie. Enfin, avec la prise en compte grandissante de la notion d’énergie grise, ces investissements pourraient s’avérer doublement bénéfiques : en plus d’assurer un gain énergétique (et donc économique) à l’industriel, ils pourraient se transformer en argument de vente, mettant en avant le caractère sobre et efficace de la chaîne de fabrication. |
- Insee
- Insee
- SOeS, Ministère du développement durable, disponible sur : www.statistiques.developpement-durable.gouv.fr/energie-climat/r/industrie.html?tx_ttnews[tt_news]=21083&cHash=fb5b458ff78e44f761db201e5f4a2641
- Indice de la production industrielle, Insee, disponible sur : www.insee.fr/fr/bases-de-donnees/bsweb/serie.asp?idbank=001654235
- Tableaux des consommations d’énergie en France, ministère de l’Économie, des Finances et de l’Industrie, 2000, disponible sur : www.industrie.gouv.fr/energie/statisti/tcef2000.htm
- L’industrie en France en 2007, Insee, disponible sur : www.insee.fr/fr/ffc/docs_ffc/ref/indfra07c.pdf
- Gisement des opérations transverses, Ceren, disponible sur : www.google.fr/url?sa=t&rct=j&q=&esrc=s&source=web&cd=2&ved=0CCgQFjAB&url=http%3A%2F%2Fwww.corpevents.fr%2FSEF2012%2Fpresentations%2Fjeudi%2Ftr5%2FFrancois%2520Bourriot.ppt&ei=gSeRVb6GDIKrUd7Mg4gJ&usg=AFQjCNEpsar3mbPswdMy8qpo-D2ygpx46A&sig2=vmaLbyrGv7sckWcCcEpEBg&bvm=bv.96783405,d.bGg
- Global Industrial Energy Efficiency Benchmarking, UNIDO, 2010, disponible sur : www.unido.org/fileadmin/user_media/Services/Energy_and_Climate_Change/Energy_Efficiency/Benchmarking_%20Energy_%20Policy_Tool.pdf
- Ademe, disponible sur : www.ademe.fr/bilan-national-recyclage-2003-2012
- Ici on entend par taux de recyclage le taux de matières venant du recyclage sur l’ensemble de la production (52 % de l’acier produit est issu du recyclage).